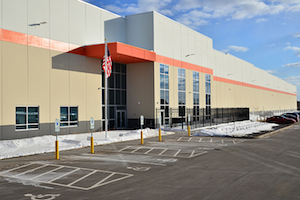
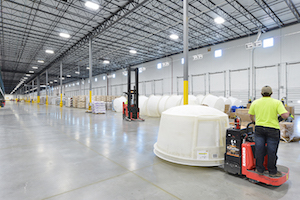
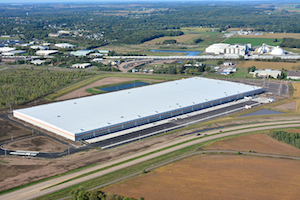
How to heat a high-bay facility with 80 overhead doors and sub-zero temperatures
Temperatures in Northern Wisconsin can dip well below freezing, sometimes for weeks at a time, during their notoriously long winters. Keeping employees comfortable in high-bay buildings on these bitter cold days isn’t easy, and energy costs can skyrocket despite facility managers’ efforts to find the most efficient way to warm hundreds of thousands of square feet or sometimes more than a million square feet of space.
Planners for the Mills Fleet Farm Distribution Center in Chippewa Falls, Wisconsin, faced this very issue. Brock Norman, project manager at Ryan Companies, stressed the need for high-efficiency heating in the 1.2 million square foot building. Besides the sub-zero winter temperatures, another concern was that the 80-plus overhead doors along the building’s perimeter would be opening and closing throughout the day.
“They were looking to maintain 60 degrees inside when it’s minus 25 degrees outside, with large bay doors opening frequently,” said Jeremy Wedel of Allan Mechanical. “We recommended Cambridge Air Solutions’s space heating and ventilation units because of their ability to operate extremely efficiently. People are used to seeing infrared and unit heaters in these buildings, but those were not going to provide the best efficiency.”
Allan Mechanical specified eight Cambridge S-Series HTHV (high temperature heating and ventilation) units. The facility was completed in March 2018, when temperatures were still quite cold. Visitors and employees noticed the comfortable temperature right away.
“The finished product produces a nice warm, EVEN heat throughout the space with easy-to-operate controls,” Norman said.
Rusty Keller, resident maintenance manager for Dematic Corp., agreed. He is facility manager for the Fleet Farm building. “The Cambridge units in our facility keep us up and running in a comfortable environment even when it is minus 10 outside,” he said.
“Everyone was surprised at how warm the Cambridge heaters keep the space,” Wedel said.
During the construction phase, the ventilation feature offered a great advantage, according to Norman. “The Cambridge products were great for construction temperature heat because they include 100 percent outdoor air ventilation. There was zero dust or debris run through the units and they brought fresh air in during construction for the rest of the trades while they worked,” he said.
Randy Niederer, Cambridge marketing director, says the company’s HTHV products feature a unique blow-thru design that allows more usable heat and thermal comfort with minimal temperature variation throughout the heated space. “Discharge air from the S-Series creates a large volume of fresh, warm air flowing throughout the building which eliminates higher ceiling temperatures and uncomfortable drafts,” he said. “Plus, the system uses 100 percent fresh air to dilute contaminants generated within the building. This virtually eliminates air quality problems associated with infrared heaters or conventional air heating systems that recirculate indoor air.”
According to a study from the Department of Energy, HTHV technology is 20 percent more energy efficient than unit heaters. Cambridge building studies illustrate as much as 70 percent better energy efficiency compared to other types of indirect and direct gas-fired systems used to heat large commercial and industrial buildings.
More than 37,000 system installations have been completed using Cambridge equipment and 2.5 billion square feet of buildings have been affected positively. “We’re committed to helping customers provide an improved working environment for people on the factory or warehouse floor,” Niederer said. “More and more building owners want improved indoor air quality and even temperatures for their employees as well, so we’re working to educate customers on the advantages of HTHV.”
Cambridge is an active member of the DOE’s Better Buildings Alliance, an initiative of manufacturers and businesses dedicated to reducing energy consumption in commercial spaces by a minimum of 20 percent by the year 2020.