Written By: Tom Cleary (R&D Manager), Dale Witte (R&D Engineer), Matthew Sides (R&D Engineering Tech)
ABSTRACT
When switching from typical natural gas, which can include up to 5% hydrogen, to natural gas blends with higher percentages of hydrogen, the most likely areas of failure are due to materials, compatibility, and combustion.
Leveraging component manufacturers' certifications and testing funded by CSA, it was found that all Cambridge heaters are compatible with natural gas blends up to 30% hydrogen.
Additionally, testing on combustion (including ignition testing, flame strength, and products of combustion) proved that Cambridge HTHV Technology, specifically the S400, on natural gas blends up to 30% hydrogen performed with similar results.
INTRODUCTION
Carbon reduction initiatives and funding are expanding across the United States. For many large, ductless buildings, Cambridge equipment has reduced both the total carbon dioxide emissions produced and overall energy usage (Reference: Cambridge Air Solutions White Paper “Gas vs Electric 2023”), but traditional gas heating systems face limitations when it comes to meeting certain decarbonization standards. That is, however, unless alternative fuel sources, such as hydrogen, are explored.
One significant advantage of hydrogen is its potential to be produced from renewable energy sources and water, emitting only water when burned.
Given our deep-rooted involvement in the heating and energy industry, it is imperative for us to take a proactive stance in spearheading the transition to these new fuel technologies.
Natural gas utilities are also exploring hydrogen as a means to decarbonize the energy they provide. The introduction of hydrogen into the natural gas supply offers a pathway for utilities to leverage the existing pipeline infrastructure while taking significant strides towards decarbonization. However, before this transition can be implemented on a large scale, further testing is imperative.
We can actively contribute to the advancement of hydrogen heating technology by sharing our test findings with gas utilities and the Canadian Standards Association (CSA). Our testing endeavors aimed to ascertain whether our products meet operational standards when utilizing hydrogen-methane blends. Initially focusing on our S400 model, we conducted tests using premixed cylinders containing varying volumes of hydrogen (10%, 20%, and 30%) balanced with methane to replicate real-world hydrogen-natural gas mixtures. The subsequent report details our findings.
SAFETY
Common safety concerns with hydrogen are increased flammability and ignitability. When hydrogen is blended into natural gas at low pressures and concentrations, the mixture acts more like straight natural gas than straight hydrogen. This mitigates most of the concerns of hydrogen. Utilities and testing agencies have suggested 30% as a maximum but are aware that some equipment may not operate properly on mixtures as low as 10% (Ref: CSA Hydrogen Working Group). For safety concerns 30% mixture and below 72PSI is still considered low. Table 1 shows the change in properties for a 20% addition of hydrogen (Ref: Properties of Hydrogen… presented by ATCO).
Table 1: Properties of Hydrogen and Natural Gas
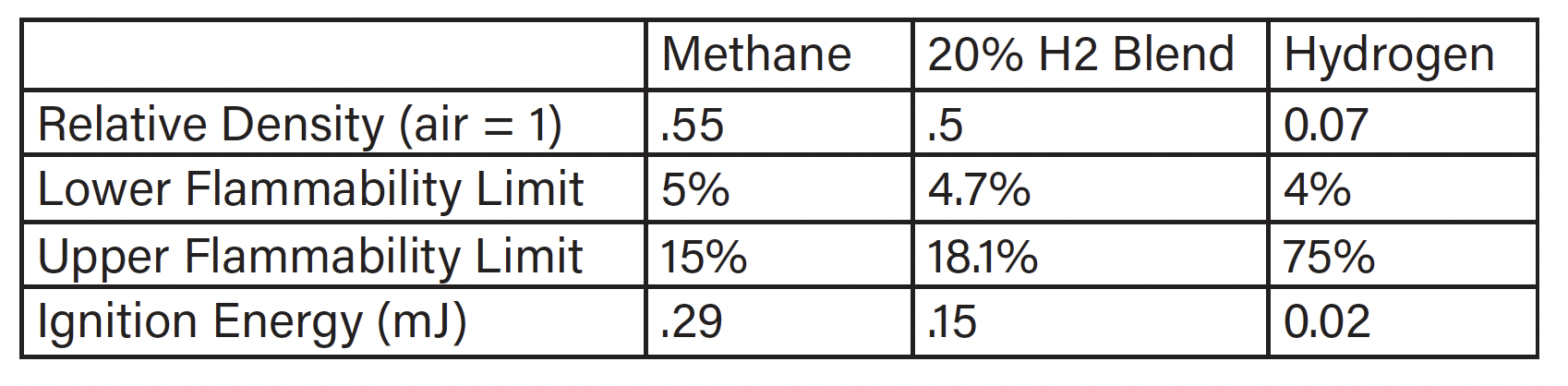
While basic fuel properties can address some concerns, others, such as leak rates, material compatibility, including Hydrogen embrittlement, and controls compatibility, require further investigation.
When possible, we verified with manufacturers that components were compatible up to 30% hydrogen. The modulating valve, ball valves, and flame safety relay were all verified this way. For common components and assembly concerns, such as iron pipe and gas trains, we leaned on experts in the industry.
The ISO gas controls group presented CSA testing that addressed the two major concerns of leakage and hydrogen embrittlement. These tests showed even large leak risks can be mitigated by a small amount of air ventilation (0.1 air exchanged per hour) in moderately sized spaces (15ft x 15ft x 15ft). Larger spaces produce even less risk. Additional testing left sample materials in pressurized hydrogen up to 72 PSI. The tests showed that cast iron pipe and many other common materials were suitable for use and did not show meaningful hydrogen embrittlement.
Hydrogen is already being mixed into existing pipeline networks in parts of Europe and North America.
Some areas in Europe are already adding up to 20% hydrogen. CSA has a formal interpretation that recognizes standard natural gas as having up to 5% hydrogen. Through this common usage, the testing presented and general research, we have concluded that our test unit can operate with up to 30% hydrogen by volume without any changes being made to the control systems or component design for safety concerns.
TESTING
Testing was based on Cambridge Air Solution’s periodic testing which follows CSA requirements for non-recirculating direct gas-fired heating and forced ventilation appliances for commercial and industrial applications (Ref: ANSI Z83.4-2017 - CSA 3.7-2017). This is a series of tests to audit the ongoing performance of a product line.
This periodic testing covers 25%, 50%, 75% and 100% of maximum allowable temperature rise which is 160°F for the Cambridge S400 model. The flame was stable across all tests and down to minimum fire which is even lower than the 25% test.
Ignition testing was also done at all temperature rises with 25 cold and 25 hot ignitions in which there was no noticeable difference between the hydrogen blends and 100% natural gas. These tests were completed at all blends (10%, 20% and 30% hydrogen) and no issues were found.
In addition to the typical periodic testing, the unit was monitored to make sure it operated normally. The testing showed that the S400 could modulate on its own to achieve our normal 160°F discharge temperature. Also, the flame detection through the Fenwal flame safety relay was virtually the same between 100% natural gas and all hydrogen mixtures tested.
EMISSIONS & GAS FLOW
CSA limits the emissions rise of carbon dioxide (CO2), carbon monoxide (CO), and nitrogen dioxide (NO2) through a heater. CO2 is calculated based on fuel, while CO and NO2 are measured.
One of the primary drivers for introducing hydrogen into natural gas is to reduce carbon emissions.
CO2 is a calculated value based on the fuel. When calculating the CO2 emissions, the value is based on the rate of fuel consumption and total air throughput. Hydrogen has an energy density of about one-third of methane, the primary component of natural gas, thus as you increase the amount of hydrogen blended with methane or natural gas the overall energy density drops (see Table 2). To maintain the same temperature rise of the furnace as the percentage of hydrogen increases, more fuel flow is needed to account for the overall decrease in energy density. The observed increase in gas flow as a function of hydrogen is illustrated in Chart 1.
Table 2: Energy Density
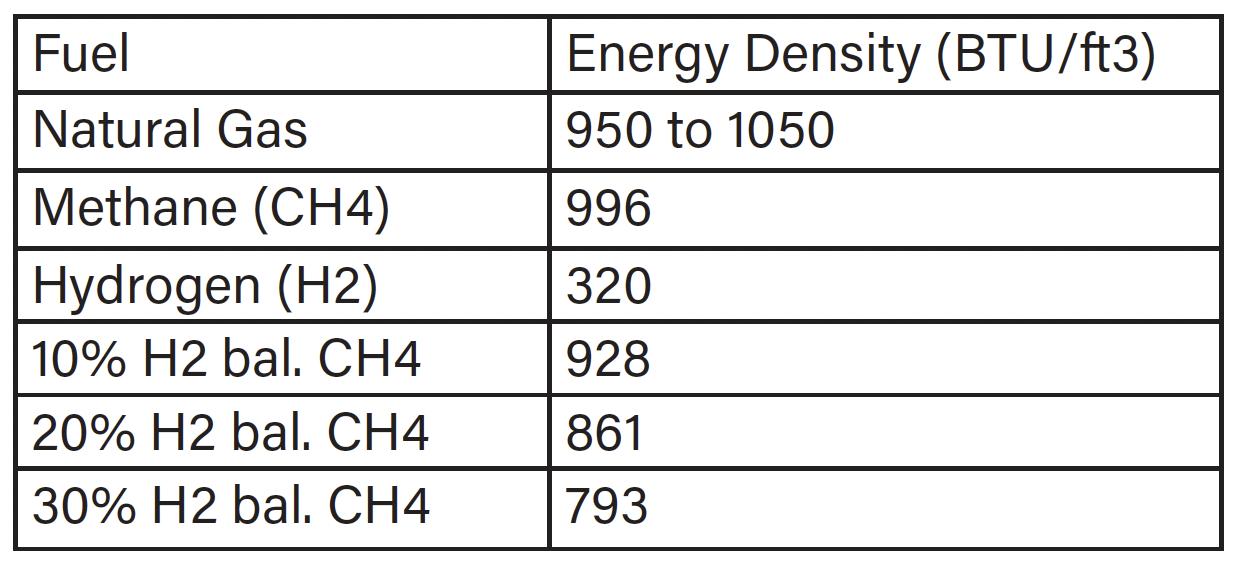
Note: Hydrogen blends are percentage by volume
Chart 2, arguably the most important, shows the decrease in CO2 emissions with increased hydrogen.
The observed decrease in CO2 emissions correlates with the percent hydrogen added; i.e., for 10, 20, and 30% admixtures the reduction of CO2 emissions is approximately 3.4, 7.3, and 12.1% respectively.
Charts 3 and 4 show the CO and NO2 emissions respectively. For both CO and NO2 emissions, the observed rise over ambient is similar to straight natural gas and all measured points are presented relative to the maximum natural gas value at the maximum temperature rise.
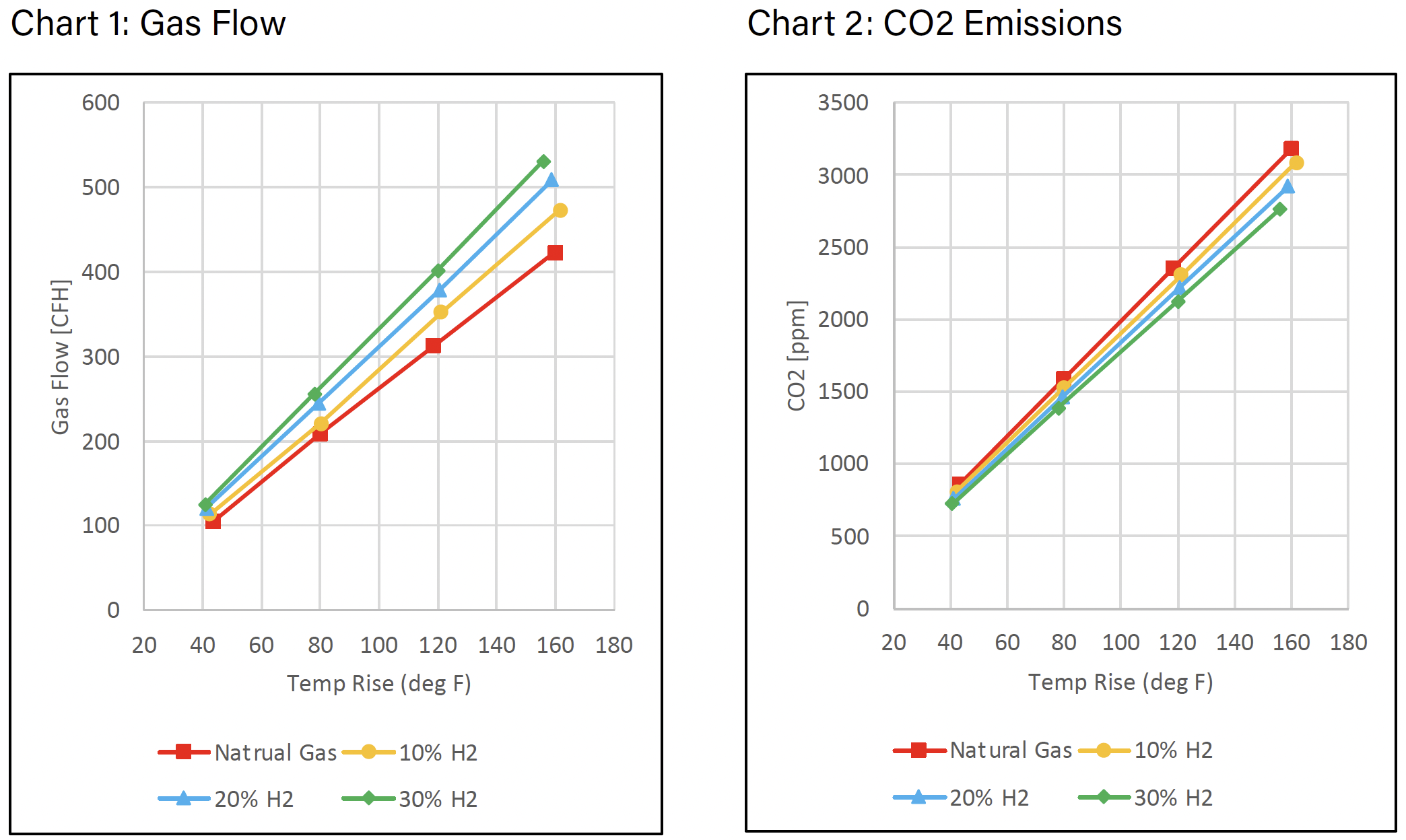
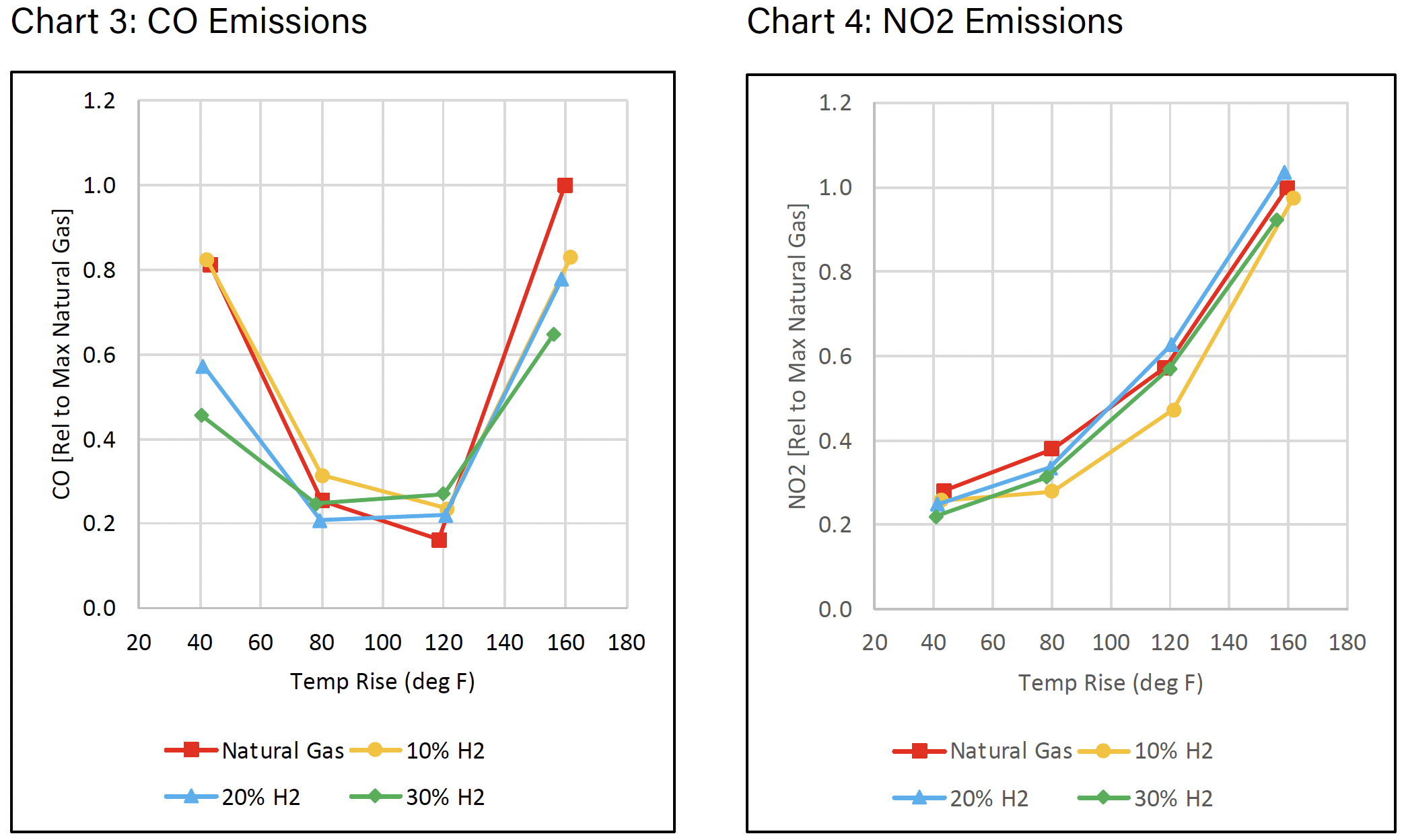
PRODUCTION & COST OF HYDROGEN
While hydrogen stands as the most abundant element in the universe, it’s not naturally present in its gaseous form on Earth. Nevertheless, its potential as an environmentally friendly alternative to fossil fuels is significant, given that its combustion only yields water. Presently, the bulk of hydrogen production relies on methods like Steam Reforming or Pyrolysis of natural gas, as well as Electrolysis of Water.
Steam Reforming, though energy-efficient, falls short in terms of environmental friendliness due to its substantial CO2 emissions per kilogram of hydrogen produced. On the other hand, Pyrolysis generates solid carbon as a byproduct, thus eliminating greenhouse gas emissions. Electrolysis, particularly when powered by renewable sources like solar and wind, produces no CO2 emissions, yet its electricity-intensive nature makes it economically challenging.
High-temperature electrolysis, employing both heat and electricity, enhances water splitting efficiency. Nuclear reactors emerge as promising candidates for providing the consistent heat and electricity essential for producing clean hydrogen, potentially opening up new markets for nuclear power plants (Ref: energy.gov, “3 Nuclear Power Plants Gearing Up for Clean Hydrogen Production”).
Irrespective of the production method, Cambridge is poised to adapt to the increasing flow of hydrogen within natural gas infrastructure.
CONCLUSION & NEXT STEPS
Cambridge has long championed energy efficiency as a means to mitigate carbon emissions, outperforming even some of the cleanest technologies available. By embracing lower carbon fuels, such as hydrogen mixed with natural gas, Cambridge can make further strides in reducing carbon dioxide emissions.
The evaluation of the S-Series indicates that it is poised to accommodate hydrogen with minimal adjustments. The readiness of our technology to embrace hydrogen is not a significant concern; rather, the pace of introducing hydrogen products may be influenced by factors such as utility infrastructure, cost considerations, and adherence to local regulations.
While our initial testing and safety assessments have been promising, they are based on a limited data set. Therefore, our next course of action involves delving deeper into the market landscape and conducting a more comprehensive testing regimen to validate these findings. This iterative process ensures that our advancements in energy efficiency align with safety standards and market demands.
If you’re interested in learning more about our technology, reach out to your local representative for further information!
DOWNLOAD WHITE PAPER PDF